Keeping a commercial boiler is crucial to the performance, safety, and constant energy conservation in an organization. A good-condition boiler has a higher efficiency and chance of avoiding scenarios whereby it fails and thus interrupts business proceedings. This paper offers an extensive analysis of the optimal protocols for commercial boiler repair and shall be useful to facility managers and servicing personnel.
Introduction to Commercial Boiler Maintenance
It is important to schedule commercial boilers’ maintenance to keep them in good shape to deliver the needed services in the commercial markets. There are these systems, central to keeping the environment habitable and operational, for uses including heating and production, say, hot water. Failure to maintain equipment right can lead to downtimes that might be very hard and expensive to address, not to mention the fact that it will not be safe and efficient enough to pass through the legal and set requisite standards. Lack of maintenance of the boiler can translate to highly expensive costs such as high energy use and costly repairs.
Regular Maintenance Schedule
Scheduled maintenance is key to increasing the efficiency of commercial boilers in their operations. Maintenance activities could be daily, weekly, or monthly, or based on the type of boiler in use or the circumstances under which the boiler is operating. Here is a suggested maintenance routine:
- Daily Checks: There should be daily rapid assessments, which focus on simple benchmarks critical for operations. This includes observing the water level, and any strange sound and also checking the pressure gauges.
- Weekly Tasks: Valves must be checked, burner inspected and safety devices must be tested as the weekly maintenance schedule of the furnace. Such a frequency ensures quick identification of possible problems.
- Monthly Maintenance: Some of the time-bound safety checks that can be done every month include testing limit controls, proper combustion function checks, and checking on blowdown systems.
- Annual Inspections: In addition, it is necessary to pose professional checks no less than one time per year. These should have to be effected by certified technicians who will examine and assess the boiler system in detail.
Maintenance Checklist
Developing a detailed maintenance checklist can significantly streamline boiler upkeep. Key tasks to include are:
- Checking Safety Controls: Check that all devices required to shut the boiler down in an emergency also work, for example, low water cut-off and pressure relief valves. This helps to minimize shocks, with such consequences as catastrophic failures.
- Inspecting the Burner and Combustion Chamber: Often the burner and the combustion chamber should be cleaned and inspected for signs of soot. It is therefore very important to maintain a clean burner to avoid inefficient combustion and high emissions.
- Flushing and Cleaning the Boiler: There are also several flushes, one of the most important is to clean the scale and sludge which hinder normal operation and cause overheating. It is therefore important to maintain the fireside area and waterside area if it has to work effectively.
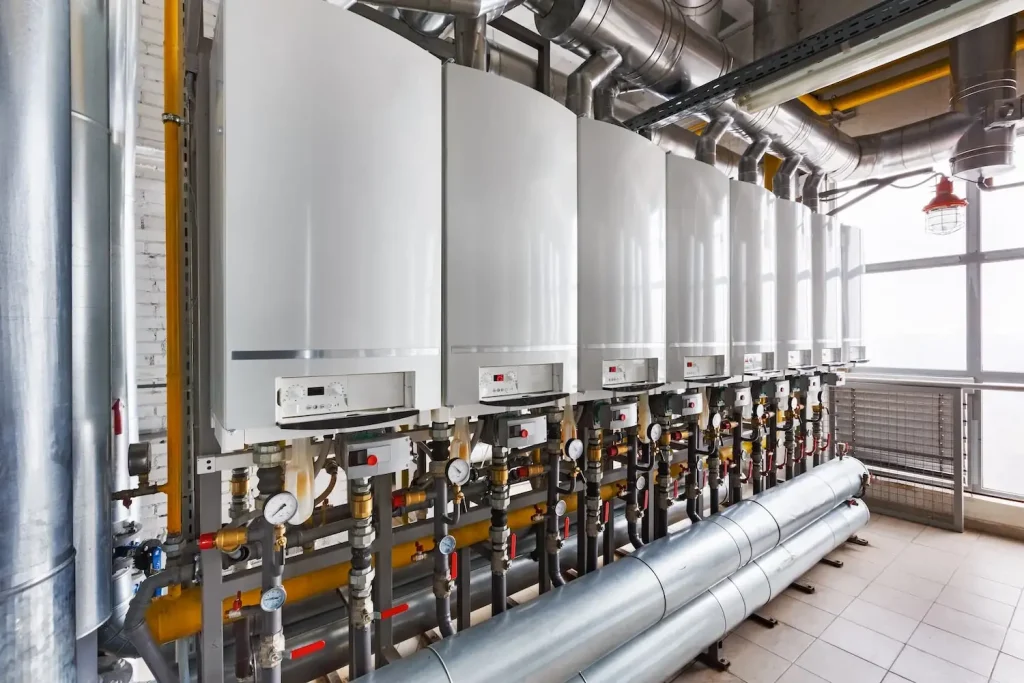
Signs of Potential Issues
This means that being very careful and observing any signs of fault in a boiler will go a long way in ensuring that when it develops a fault, it is not a very big problem that could have caused havoc. Here are common indicators to watch for:
- Unusual Noises: Any type of noise ranging from gurgling, popping, or banging could be a result of the build-up of sediments or pressure complications. These should therefore be conducted as soon as possible to prevent aggravation of the condition.
- Error Codes: Of these modern boilers used today, most of them come with display features that alert users to operational faults. By coming across these codes one can check for any malfunction in a very short time.
- Leaks and Water Pooling: Boiler system leakage is not allowed; any sign of leakage or water standing around the equipment should be halted since they are a sign of something wrong.
Importance of Professional Inspections
Engaging certified professionals for annual inspections is a regulatory compliance issue and a best practice in maintaining boiler safety and functionality. Regular expert evaluations have numerous benefits, including:
- If performed comprehensive assessments safety hazards that may culminate to failures can be pointed out.
- Industry feedback on potentials for repair or modification and additional methods for even further boiler service durability.
- Security that the boiler is safe in the way it works and energy efficient in the way it produces heat.
Energy Efficiency Tips
The management of operational costs for commercial boilers can be greatly minimized by optimizing their operations. Here are some practical tips:
- Upgrade Insulation: To reduce the heat loss from pipes and the boiler, its insulation quality should be enhanced and the system insulated.
- Implement Energy-Saving Devices: There should be some ideas on hiring smart thermostats and zone control to reduce the output that is needed based on its demand in every region and improve on the energy gains.
- Regular Tune-ups: It is also important desirably to program timely burner control and maintenance to allow optimum combustion and minimize universal fuel waste.
Frequently asked questions on commercial boiler maintenance
Frequency of boiler maintenance, cost related to it, and energy efficiency rebates are some of the queries that facility managers generally come across. Addressing these inquiries can provide clarity and improve maintenance practices:
- How frequently should I be to have my boiler serviced?
An annual check-up by a professional technician is advisable. This type of heating may, however, require more frequent maintenance depending on the usage and or the manufacturer’s recommendations.
- Concerning the commercial boiler maintenance, what kind of costs may be faced?
The price depends on the type and extent of service, the intricacy of the boiler system, and if parts need to be replaced.
- Is there any rebate regarding energy efficiency?
Homeowners and many small businesses get rebates from utility companies and government programs for upgrading their boilers to modern efficient ones or for installing energy-efficient technologies.
Conclusion
Maintaining these commercial boilers is essential if one aims at getting a smooth, cost-effective, and safe system. This means fixing easy problems within the fixed timeline, and use of professional services to ensure that the boiler system is effective in the facilities. Boiler maintenance needs to be done soon or the best time to talk to a reputable service provider needs to be availed today by facility managers.