Special inspections are critical to modern construction, ensuring that structures meet stringent safety, quality, and compliance standards. Unlike routine inspections, special inspections focus on specific materials, such as fire-resistant materials, systems, or processes that require expert verification due to their complexity or importance to structural design and integrity. These inspections are mandated by building codes and play a vital role in risk mitigation, regulatory compliance, and long-term project success.
Read on to learn common types of special inspections in constructions and why they matter.
The Importance of Special Inspections
Construction projects involve numerous high-stakes elements, from foundational work to fireproofing and seismic reinforcements. Without proper oversight, flaws in these areas can lead to catastrophic failures, costly repairs, or even legal liabilities. Special inspections can help identify potential issues early, ensuring corrective actions are taken before they escalate.
Below are some of the most common types of special inspections in construction and their significance:
Structural Steel and Welding Inspections
Structural steel forms the backbone of many modern buildings, making its integrity non-negotiable. Inspections performed by special inspectors for steel construction typically include:
- Welding Quality: Certified inspectors check welds for cracks, porosity, and incomplete fusion to ensure structural integrity and prevent potential failures.
- Bolted Connections: Inspectors ensure bolts are correctly tensioned and aligned to maintain structural stability and prevent loosening or joint failure under load.
- Material Verification: Inspectors verify steel grades match design requirements to guarantee structural strength and prevent overstressing critical load-bearing and other structural components.
By conducting a special inspection, structural weaknesses could be discovered, preventing the risk of collapses or premature deterioration.
Concrete Placement and Testing
Concrete is one of the most widely used construction materials, but its performance depends heavily on proper mixing, pouring, and curing. Some key inspection areas in concrete construction include:
- Slump Tests: Inspectors conduct slump tests to verify concrete workability, maintaining proper consistency and preventing material separation during placement.
- Compressive Strength Tests: Compression tests on concrete cylinders verify strength compliance with engineering specifications, ensuring structural safety and performance standards are met.
- Reinforcement Placement: Before concrete is placed, inspectors verify that rebar placement meets design specs for proper load test procedures and distribution, corrosion protection, and structural integrity.
Inadequate concrete inspections can result in cracking, spalling, or structural failure under load.
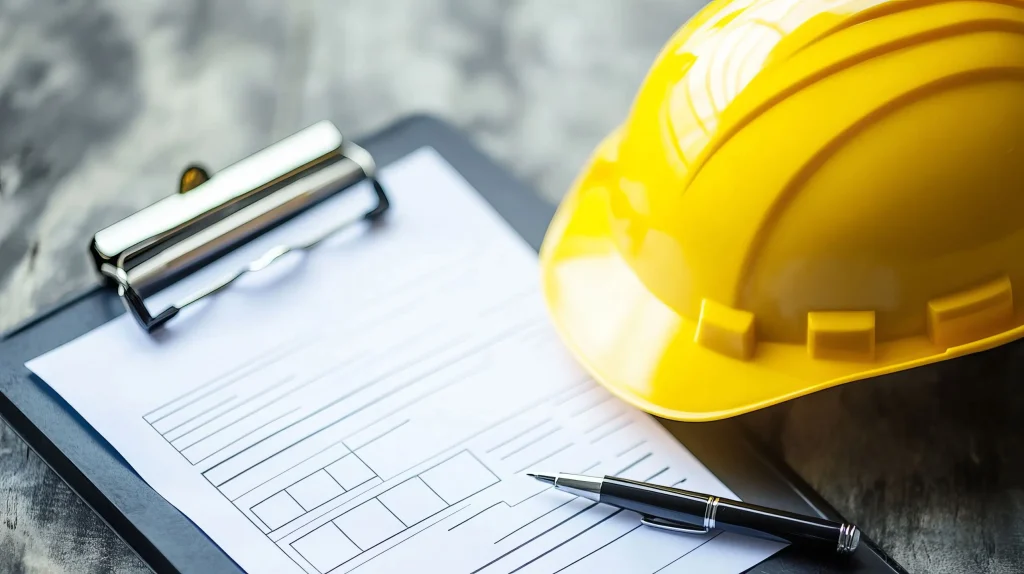
Masonry and Grout Inspections
Masonry construction requires precise workmanship to ensure durability. Special inspections for masonry focus on the following:
- Mortar Mix Proportions: Inspectors confirm mortar mix proportions meet specifications since improper ratios compromise adhesion, reducing masonry’s structural durability and weather resistance.
- Grout Placement: Inspectors verify grout fills masonry cavities to create solid reinforcement, preventing voids that could compromise foundation wall strength and stability.
- Foundation Wall Alignment and Reinforcement: Inspectors use levels and flow measurements to confirm walls are perfectly vertical and reinforcement placement matches structural drawings for optimal load-bearing capacity.
Poor masonry inspections may lead to water infiltration, thermal inefficiency, or seismic vulnerability.
Fireproofing and Life Safety Systems
Fire resistance is a critical safety requirement in commercial and multi-family buildings. Inspections cover the following:
- Spray-Applied Fireproofing (SFRM): Thickness and adhesion tests ensure adequate protection for steel elements.
- Firestopping: Inspectors verify that penetrations (e.g., pipes, cables) are properly sealed to prevent fire spread.
- Smoke Control Systems: Ensuring dampers and ventilation operate as designed during emergencies.
Neglecting fireproofing inspections compromises occupant safety and violates fire codes.
Seismic and Wind Resistance Inspections
In earthquake-prone or high-wind regions, special inspections are essential for:
- Shear Wall Installations: Inspectors validate shear wall bracing and fastener installation to ensure seismic resistance and structural stability during lateral force events.
- Diaphragm Connections: Inspectors verify diaphragm connections are properly installed to effectively distribute wind and seismic loads throughout the building’s structural system.
- Anchor Bolts and Hold-Downs: Inspectors confirm anchor bolts and hold-downs are properly installed to prevent uplift and ensure structural stability during seismic events.
These inspections are vital for preventing catastrophic damage during natural disasters.
Soil and Foundation Inspections
A building’s stability starts with its foundation. Inspections include:
- Soil Testing: Inspectors conduct soil density tests and bearing capacity analyses to verify ground stability meets structural foundation requirements before concrete placement.
- Deep Foundation Verification: Checking piles or caissons for proper installation and load transfer.
- Waterproofing and Drainage: Preventing moisture-related issues like settling or mold growth.
Foundation failures are among the costliest construction defects, making the special inspections process indispensable.
Energy Efficiency and Envelope Inspections
Modern buildings must comply with energy codes, requiring inspections for:
- Insulation Installation: Inspectors verify insulation installation achieves complete coverage and specified thermal resistance values to meet energy code performance requirements.
- Air Barrier Systems: Inspectors conduct air barrier tests to identify leaks that compromise thermal performance and increase energy consumption in climate-controlled spaces.
- Window and Door Sealing: Inspectors verify continuous insulation and proper sealing at fenestrations to minimize heat transfer and air infiltration through building envelopes.
Deficiencies here lead to higher utility costs and reduced occupant comfort.
Why Special Inspections Matter
Special inspections are not just a regulatory formality—they are a proactive measure to safeguard investments, lives, and reputations. By catching errors early, they can reduce the likelihood of the following:
- Structural Failures: Inspectors verify structural integrity through rigorous testing to eliminate building failure risks that could harm residents and users.
- Costly Rework: Inspectors identify construction defects early through proactive verification, preventing costly rework and delays during later project phases.
- Legal Penalties: Non-compliance with building codes can result in fines or project shutdowns.
- Long-Term Performance Issues: Ensuring buildings remain durable and functional for decades.
Conducting special inspections can ensure the construction projects remain safe from start to finish.
Conclusion
Special inspections are indispensable in construction, from steel welding to seismic reinforcements. They provide an additional layer of scrutiny that routine inspections cannot match, ensuring compliance, safety, and quality.
By adhering to rigorous inspection protocols and detailed procedure, the construction industry can uphold its commitment to safety and excellence, one project at a time.