In industrial settings, lighting is a key component of operational success. Industrial track lighting, known for its flexibility and efficiency, boosts productivity and safety in large spaces. As tasks in manufacturing plants, warehouses, and other facilities become more complex, the need for strategic lighting is essential. Good lighting reduces errors and accidents, making the workplace safer. Understanding how industrial track lighting works is a must for improving work conditions and saving energy.
Beyond the basics, it’s important to explore how specific lighting needs influence custom setups. Here we’ll look into design principles, focusing on optimal placement by considering factors like height, angle, and spacing. Flexibility is also essential, as industrial spaces often change over time. Additionally, we’ll cover key aspects of installing industrial track lighting, emphasizing safety and efficiency to ensure a durable and cost-effective system.
Industrial Track Lighting Basics
To understand the basics of industrial track lighting, it’s important to know its main parts and benefits. Unlike regular lighting, track systems have a series of lights attached to a continuous track, giving you great flexibility and control. You can easily move and adjust the direction of the lights, making them perfect for large, changing spaces where tasks and layouts often shift. Track lighting is built to improve both function and appearance, meeting the specific needs of factories, warehouses, and similar places.
Compared to fixed ceiling lights or incandescent bulbs, track lighting stands out for its flexibility. Knowing these basics helps you make better decisions when choosing a setup that fits your industrial space. Understanding the types of tracks (J, H, or L) and power sources will ensure you pick a system that works well for your needs.
Assessing the Needs of Your Space
Each industrial space has unique lighting requirements, so it’s important to assess your facility’s specific needs when planning track lighting. Start by analyzing the tasks performed in different areas, as activities like precision work may require brighter, focused lighting, while general storage areas could benefit from softer, more even light.
Consider the layout of your facility: workstations, assembly lines, or shipping docks might need tailored lighting solutions to ensure optimal visibility and safety. Also, plan for future expansions or changes in operations that could affect your lighting needs. Additionally, energy efficiency should be balanced with the lighting intensity to reduce costs while maintaining effectiveness.
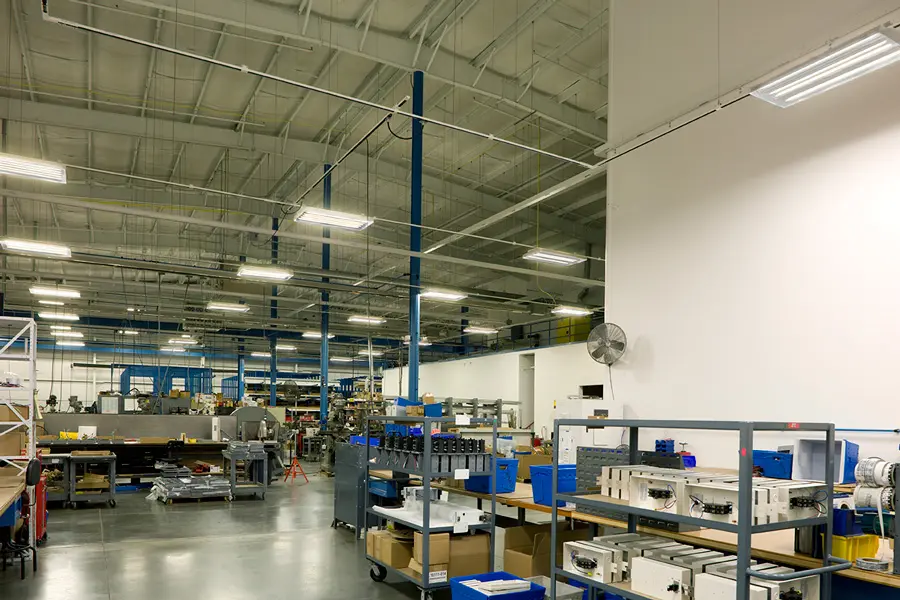
Design Considerations for Optimal Positioning
For optimal track lighting placement, it’s important to understand key design principles. The height of the lights is essential; mounting them too high can spread the light too broadly, reducing intensity, while mounting them too low can create harsh shadows and cause strain. The angle of the lights also matters: positioning them correctly can highlight areas without causing glare.
The spacing between fixtures affects how evenly the light is distributed. Lights placed too close together can overlap and create excessive brightness, while lights too far apart can leave dim areas. By considering these factors, you can achieve even lighting that reduces shadows and improves efficiency in industrial settings.
Incorporating Flexibility in Lighting Design
Adjusting to changing industrial environments requires a flexible approach to lighting design, helping facilities stay adaptable to shifting needs and layouts. A versatile lighting plan ensures lasting functionality and convenience, key in fast-moving settings where demands change quickly. Systems like track lighting allow for easy fixture adjustments and lighting changes with minimal disruption.
This flexibility not only saves costs by avoiding frequent upgrades but also improves efficiency by providing the right lighting for different tasks and spaces. A well-planned lighting design also supports future expansions or reconfigurations, aligning with long-term goals.
Safety and Efficiency in Lighting Installation
Installing lighting systems correctly is key for both safety and efficiency in industrial settings. Secure fixtures help prevent dangers like electrical faults or falling lights, which could harm workers and interrupt operations. Safety steps should include checking connections and using the right mounts for the weight and type of fixtures. Energy efficiency is also important, and using LED lights is a good option due to their long life and lower energy use.
Placing lights thoughtfully can reduce energy costs by avoiding over-lighting and focusing light where it’s most needed. Adding smart controls that adjust lighting based on occupancy or time of day can further save energy.
Industrial track lighting goes beyond simply brightening spaces; it improves productivity, safety, and efficiency in demanding environments. By assessing the unique needs of each facility, businesses can tailor lighting setups to improve visibility and reduce errors. Thoughtful design choices, such as optimal positioning and spacing, ensure even lighting distribution while minimizing shadows and glare. Incorporating flexibility allows for easy adjustments as operations progress, making it a long-term investment. Proper installation prioritizes safety and energy efficiency, creating a well-lit workspace that supports smooth, safe, and cost-effective operations in any industrial setting.